Problem Fuels
PROBLEM CASE 1 :
The Problem
There was a ship with loss of power and drifting in open seas. The fuel pump, valves, nozzles and springs were badly damaged. The fuel had met all ISO 8217 2010 specifications including the Acid number. The ship operators wanted to find the cause of the damage. They were not customers of Viswa Lab. This problem had passed to two other labs with no conclusion and was then referred to Viswa Lab.
Viswa simultaneously received a fuel sample from a customer doing routine Peace Of Mind Package POMP testing. This customer had bunkered in the same port as the other ship.
Investigation
POMP tests the fuel for 6 additional tests which are not included in the ISO 8217 2010 tests. One of these tests is a modified pH TMdeveloped by Viswa Lab. This test is useful in determining the corrosive potential of a fuel. This modified pH identified the fuel as being highly acidic with high corrosion potential. The customer was informed of this before any damage took place. Viswa Lab also worked with the customer to provide some solutions for the use of this fuel.
The fuel from the damaged ship was evaluated using an modified pH TM. The fuel was found to be highly acidic. The fuel pump pistons were badly scratched by the corrosive nature of the fuel. All the plungers were scratched. There was also significant damage to the nozzles and valves.
Conclusion
The Acid Number in the ISO 8217 methods can sometimes miss identifying the corrosive potential of a fuel. These fuels can cause significant damage. The modified pH TM method has been developed to identify the corrosive fuels, which can be missed on the routine ISO 8217 tests. The modified pH TM is a part of the POMP package and can help identify and prevent major fuel associated damage.
Viswa Lab’s POMP tests bring additional value to the customer by intelligent and pertinent screening of fuels that meet basic requirements.
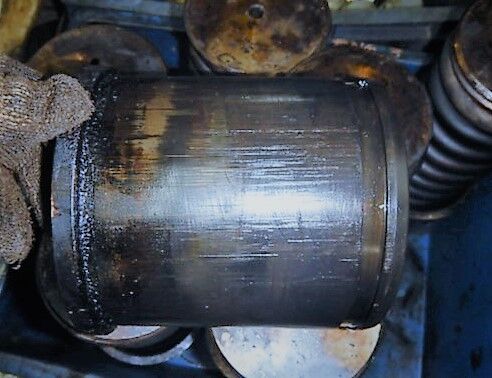
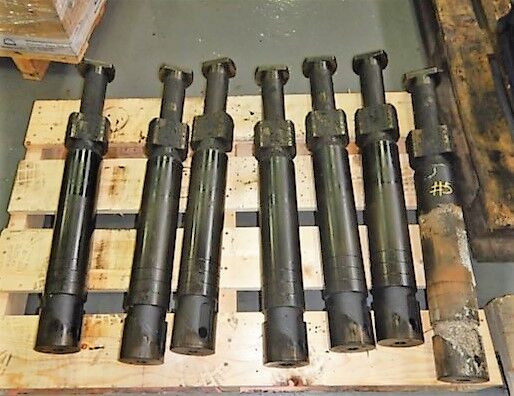
PROBLEM CASE 2 :
The Problem
There was a vessel which had initially experienced complete blockage of the filters threatening the stoppage of main engine and auxiliary engine. After this, the vessel lost power and had to be towed to the port.
Viswa Lab was asked to evaluate the machinery damage and perform the fuel testing. The damage was estimated at $2 million
Investigation
There was significant wear of the piston rings and cylinder liner of the main and auxiliary engines with arrested flexibility which led to the engines stopping. A complete fuel analysis was performed, purifier efficiency was evaluated, ignition and combustion studies were conducted, Fourier Transform Infra Red spectroscopy FTIR, Gas chromatography mass spectrometry GCMS and Filter Blocking Tendency Number (FBTN) were evaluated. Toluene insoluble was also part of the investigation.
The initial fuel analysis demonstrated high microcarbon residue MCR, high calculated carbon aromaticity index CCAI and high asphaltenes. To evaluate the filter blocking, FTIR, GCMS and the FBTN were evaluated. The FTIR indicated the presence of asphalt type material, different from asphaltene seen in fuels. The GCMS at high temperature was abnormal demonstrating the presence of very high boiling fraction (greater than that of residual fuel). This was consistent with the finding of asphalt in the fuel. FBTN demonstrated filter blocking by a carbonaceous material, consistent with the asphalt. The general theory behind Toluene insoluble is that toluene would dissolve all wax or aromatic compounds present and the left over will be something unrelated to fuel. The Toluene insoluble demonstrated carbonaceous particles which under microscopy were large.
The purifier efficiency was normal. Upon further understanding of this analysis, it was found that the purifier had been by passed because of the filter blocking. This had resulted in a large amount of asphalt entering the engine, getting deposited on piston rings, arresting the flexibility resulting in high wear of piston rings and cylinder liner. This phenomenon was repeated in Auxiliary engines as well. The damage was so severe that the vessel lost power and had to be towed to the port.
Conclusion
The problem on board the vessel was caused by the presence of asphalt combined with the residual fuel. This asphalt caused filter blocking and the later piston ring immobilization and breakage with significant liner wear. Viswa Lab worked with the customer and used the experience and years of knowledge to provide real world knowledge and solutions to the customer.
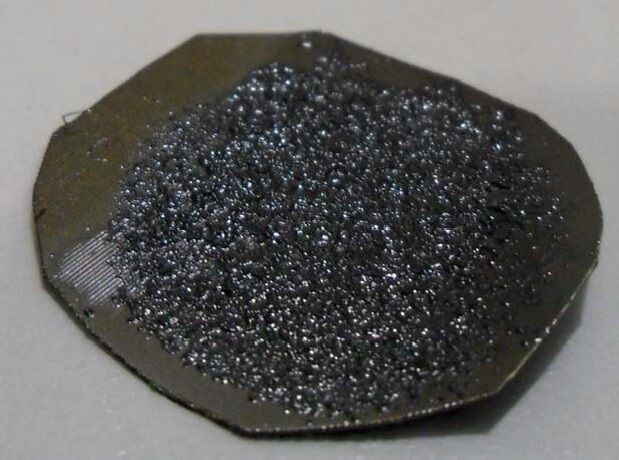
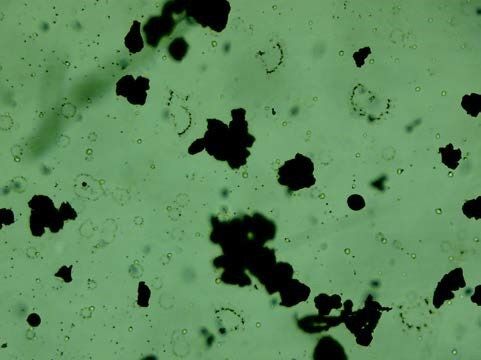
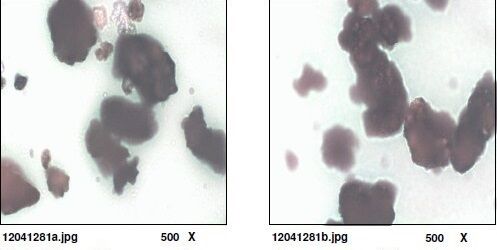
PROBLEM CASE 3 :
The Problem
A vessel using Marine distillate fuel reported filter and purifier choking. Before and after purifier samples were sent to Viswa Lab.
Investigation
The routine analysis was normal. The purifier efficiency and paraffin wax content were within normal limits. There was high bacterial contamination, which was quantified, in both the before and after purifier samples with purifier choking. The fuel had been stored for a long time before using. A complete assessment and solution along with training of procedures that should be implemented when handling distillate fuels was performed by Viswa Lab to reduce similar problems in the future.
Conclusion
Awareness of problems caused by marine distillate fuels is expanding as different problems and contaminants are being seen. Adequate settling and draining of storage tanks when fuels are stored for long times, cleaning of tanks especially those holding distillate fuels, initial testing, fuel rotation and appropriate use of additives were some of the solutions that were used in this case of bacterial contamination.
Comprehensive testing and solutions for all types of fuels can be provided by Viswa Lab so that we give the customer the best way forward to use the fuel.
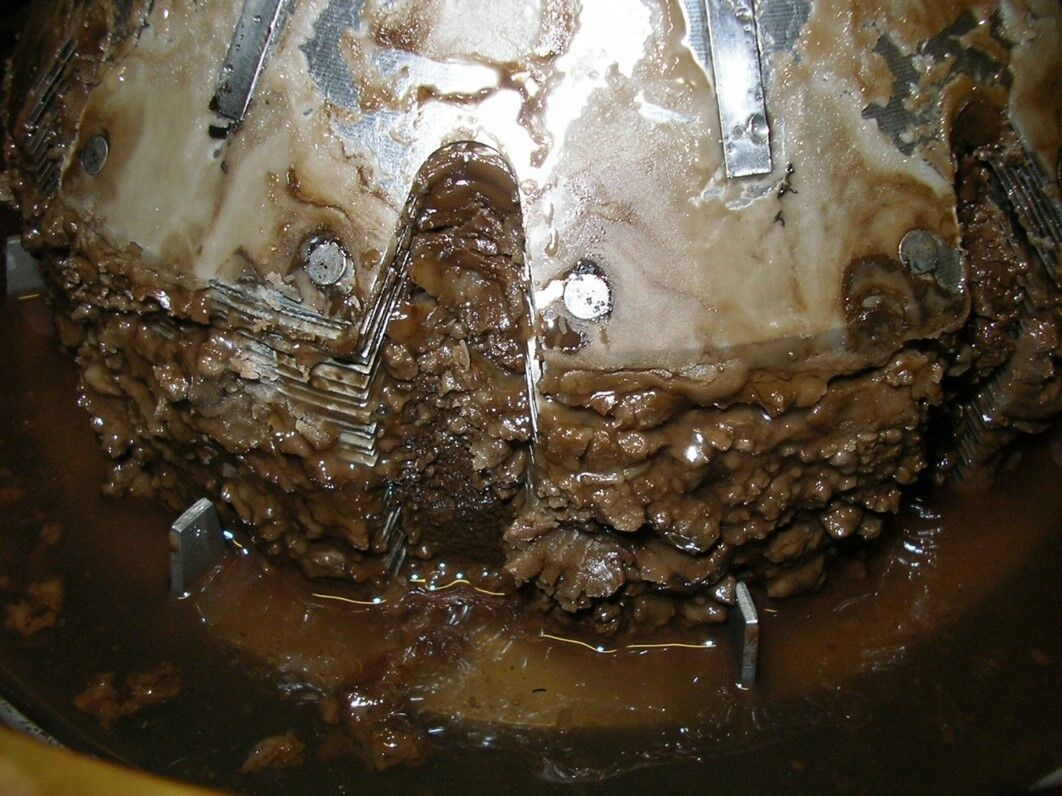
PROBLEM CASE 4 :
The Problem
Vessel using a fuel with piston ring damage, turbocharger damage and scavenge fire. The initial ISO 8217 tests had been performed at another lab and were normal. Viswa Lab was approached by the ship owner and insurance company.
Investigation
GCMS comprehensive testing, Ignition and combustion studies, modified pH TM method, Acid number were additional tests performed.
The fuel had a high microcarbon residue, high Problem Fuel Identification Number TM, and was highly alkaline. The fuel ignition and combustion properties were poor. The Cylinder lubrication was excessive which further contributed to the alkalinity.
While performing an analysis to determine the root cause, it was believed that the excess alkalinity led to removal of corrosion pits on liner generating highly polished surface and eventually leading to scuffing between the cylinder liner and piston. The poor quality fuel and highly polished liner surface and possible scuffing would have resulted in severe wear of piston rings and allowed a blowback of the hot combustion gasses through the gap between piston ring and liner and reaching the under piston scavenge space. Heavy accumulation of cylinder lube oil in under piston space also likely occurred since the cylinder lube oil feed was almost 80% more than what it should have been. The resulting scavenge fire must have spread to all the units and would have also entered the combustion space.
Conclusion
The poor quality fuel as identified by the PFIN TM and the highly alkaline nature of the fuel was the background. This was worsened by over lubrication with cylinder lube oil and accumulation in the under piston space. All of these factors likely contributed to the severe wear of the piston rings and blow back of the combustion gases, which eventually resulted in the scavenge fire.
Viswa Lab was able to test and analyze all the results to pinpoint the three converging factors in this case. The POMP tests would have identified the alkaline nature of the fuel and the higher MCR would have flagged a need for further testing for PFIN.
Viswa Lab works with all our customers to find and create solutions no matter what those Marine problems are. Viswa Lab guarantees to be a partner in basic testing, in depth testing, problem fuel analysis, solution creation, knowledge sharing and in empowerment of the customer.
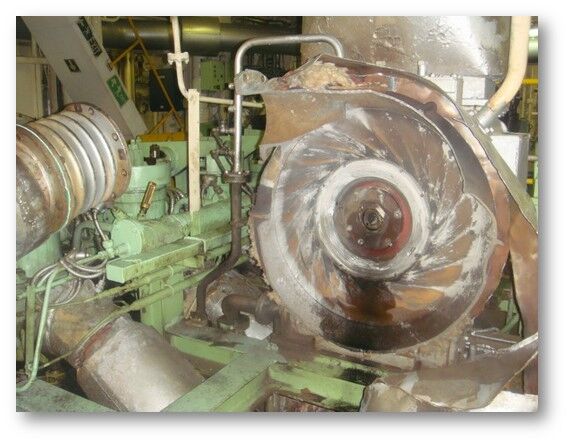
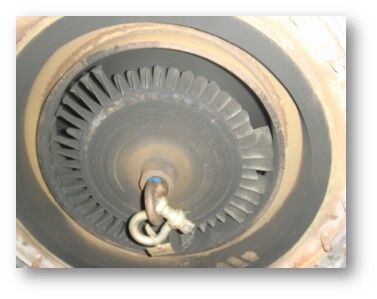
Viswa Lab Houston
12140 Almeda Rd.Houston, Texas 77045 USA
713.842.1985
Customerhelp@viswalab.com
VTIC Houston
12140 Almeda Road Houston,Texas 77045
U.S.A
713.842.1985
Customerhelp@vticservices.com
Viswa Lab Singapore
80 Tagore LaneSingapore 787501
65.6778.7975
singapore@viswalab.com
Center of excellence for The Viswa Group
Technology Information Engineering Services Pvt LtdPlot 100 - 103, Export Promotion Industrial Park,
Whitefield, Bangalore
560066
Viswa Lab UK
New First AvenueWilton International SiteMiddlesbrough, Cleveland TS104RG
44.16427331450
uk@viswalab.com
Viswa Lab UAE
Viswa Lab International FZEWarehouse 17B
Fujairah Freezone 1
Fujairah PO Box 50234
971.9228.2787
971.5274.62429
uae@viswalab.com
Viswa Lab Belgium
Administrative OfficeEmdenweg 23 (Kaai 217)
2030 Antwerp Belgium
32.3541.4441
europe@viswalab.com
VTIC Louisiana
1441 Canal Street,Suite #402
New Orleans, LA 70112
713.408.1061
504.327.9161
504.407.0464
customerhelp@vticservices.com